Dairy farmers around the world have come to expect the World Dairy Expo to highlight the latest technologies available for increasing performance and efficiency and WDE 2021 was no exception. Among the most intriguing and interesting revelations was the Smart Soaker™ (Figure 1). Created and marketed by Agpro this innovative technology offers the ability to take full command of the cooling of cows through feed line soaking by optimizing the cooling effect for the cow while maximizing the efficiency of water used in the process.
The Critical Nature of Water
We often talk about the importance of water to the dairy cow, lauding it as the most important nutrient of all and rightly so. Depending on whose number you look at, the average milking dairy cow will consume from 30-50 gallons of water each day. A cow can live for weeks without feed but will die in days without water. Water is critically important to the dairy cow in more ways than one. Beyond direct consumption of water via drinking and that which is incorporated into feed, water plays a vital role in providing cooling comfort to cows when temperatures rise. While we humans are very comfortable at 72°F (22°C) for the dairy cow as illustrated in the chart below, heat stress has already begun.1
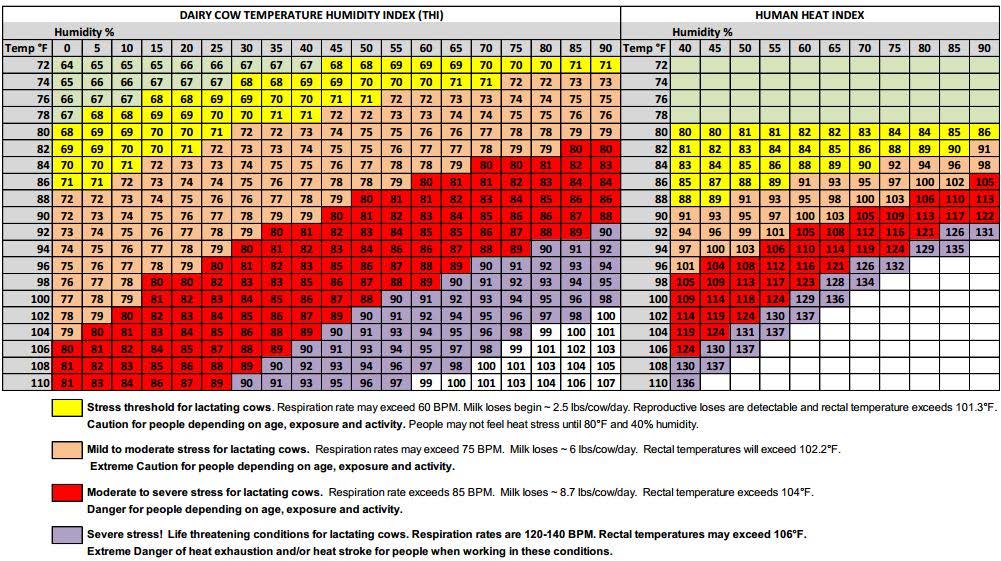
Soaking Cows at the Feed Line Works
There is little argument over the fact that soaking cows at the feedbunk during hot weather is advantageous. All research projects studying the use of soaking in milking cows has shown a marked advantage of the practice. One such research trial showed over eight pounds of milk per cow per day in increased milk production.2 We have learned that there are even huge benefits to cooling dry cows. More on that a little later.
The magic of applying water to cows in hot and humid environments is due to the science of “evaporative cooling.” Simply put, evaporative cooling is the reduction of temperature by the removal of water. The degree of cooling that takes place is highly dependent upon the humidity level in the environment. The lower the humidity, the better evaporative cooling works because “dry air” can absorb more water and do so more quickly than “wet air.” This explains why cooling the environment inside cross-vent and tunnel vent barns works best in arid climates.
In regions where both high temperature and high humidity exist concurrently, alternately soaking cows and “blow drying” with fans to facilitate the evaporative cooling process on the skin of the cow is a highly effective way to overcome high humidity levels. In fact, research has determined that even in barns (either cross-vent or tunnel vent) where evaporative cooling is used to cool the air temperature that the use of feed line soakers is highly beneficial in providing even better cow cooling due to the reduced efficiency of environmental cooling due to high humidity.3
Some Perspective
As beneficial as the evaporative cooling effect of feed line soakers combined with fans is, there is a downside. Soakers consume a large amount of water. As a result, over time dairy farmers and their advisors have looked at variables such as reducing nozzle size, increasing nozzle spacings, or manipulating cycle frequency and/or duration to save water. The reality, however, is that limiting water may also result in decreasing the cooling efficiency for the cow.
There is a wide variation in systems used to cool cows at the feedbunk. As already alluded to, there are nozzle spacings of 4, 6, or 8-foot centers, a variety of different nozzles, and another often overlooked variable – water pressure – which can drastically affect the actual water output at the nozzle. (Increasing the water pressure from 10 to 20 PSI can increase output 25-50%, for example!)
A commonly used conventional soaker system configuration in hot, humid locations utilizing nozzles with a .75 GPM rating on an 8-foot spacing that alternately cycles on and off for 3 minutes and 12 minutes respectively during a 24-hour period will use a whopping 54 gallons of water per cow per day if conditions call for soakers around the clock. For perspective, a hypothetical herd milking an average of 2,500 cows where heat stress (temperatures above 72°F – some research points to an even lower number) is prevalent as much as 180 days a year, that would amount to over 24 million gallons of water over that period. That’s enough water to cover a U.S. football field with 50 feet of water! It’s a fact that some volume of that amount evaporates depending on the prevailing ambient conditions, but it is also worth remembering that the higher the ambient humidity (which is likely when the soakers are running), the smaller the amount of evaporation that occurs. The rest of it, however, goes down the drain and into the waste/nutrient stream.
Feed Line Soaking Efficiency
The concept of soaking cows at the feed bunk has been around for decades and accomplished through a variety of application designs and techniques. While it’s not hard to evoke a lively discussion among dairy farmers, consultants, and designers as to what delivery system or soaking protocol is best, they all will agree that they would like to see more efficiency in this cooling approach.
“Efficiency” in this case refers to reducing water usage and minimizing runoff without sacrificing the benefit to the cow and ultimately the bulk tank. With ever-increasing pressures and concerns over environmental impacts (both conservation and contamination), drawing water out of the ground and turning most of it into wastewater has become increasingly more difficult to defend.
That’s just part of the problem. The public perception aspect of the issue is real but says nothing of the economics related to soaking as a means of cooling. Water is expensive to produce (especially in some regions of the world), and wastewater is expensive to dispose of, never mind the impact and negative connotations it projects to the environment, whether real or perceived. Lagoon space is precious and expensive and digging more lagoons does not address the problem.
Water Costs Both Ways
Notwithstanding the fact that there is absolutely an inherent value in the waste, the facts are that the waste/nutrient stream is a cost center. Waste disposal costs are highly variable because there are so many methods of accomplishing that task, but let’s be honest, none of them are free. Hypothetically (and perhaps conservatively), let’s assume that in the case of our earlier hypothetical herd that 50% of those 24 million gallons evaporates. That still leaves us with 12 million gallons of runoff that goes to the lagoon which must at some point be dealt with. A cursory review of literature documented the extreme variability previously mentioned but one review that included the hauling of liquids quoted a range of $.01 to $.03 per gallon. If we assume even the lowest range of $.01/gallon the bill for those 12 million gallons of liquid in our hypothetical example would be $120,000 – a cost many may underestimate or even overlook.
The nutrient stream of a dairy farm poses many challenges. Those challenges have spawned many different approaches to reducing the costs associated with dealing with that stream. While every farm is different, the first and most obvious approach regardless of individual preference for any of those systems would be to do everything feasible to reduce the creation of unnecessary liquid that ends up in the lagoon to begin with. A huge opportunity for water savings on dairy farms exists around feed line soaking.
Traditionally anything that makes cows more comfortable and increases milk production is a “no-brainer” until proven otherwise. While efforts have been made by dairy farmers around the world to reduce water usage, in the case of soaking cows at the feed bunk, few options beyond simply cutting water flow (GPM) or reducing the frequency and/or soaking time per cycle have been available. At some point, all these strategies can have a negative impact on cooling effect – that same cooling effect we are after to begin with!
Feed Line Soaking Needs New Technology
Commenting in a May 2017 industry article regarding a paper presented at the 2017 Western Dairy Conference earlier that same year, Dr. Joe Harner suggested that a savings of 75-80% in soaker water usage may be achievable if the technology to incorporate individual sensors on soaker heads that only activate when cows are in range and employ both temperature and humidity indexing (THI) in the controlling program is achieved. Noting that the economics of such technology would obviously be important, he also made note of the fact that the technology would need to be mindful of and not negatively impact feed intake.4 It appears that the Smart Soaker™ “checks all the boxes” by providing the ability to strategically control the soaking process from beginning to end and drastically increase the efficiency of the feed bunk soaking process.
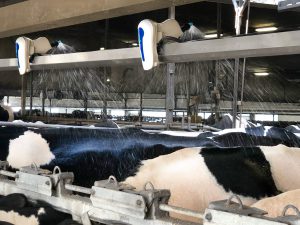
Utilizing an individual ultrasonic eye and fully programmable circuitry, the Smart Soaker™ restricts the application of precious water unless cows are present (in range), and then only when the pre-settable THI parameter is met (Figure 2). The soaking time and interval are fully programmable, managed by the user-friendly controller located in each barn. This allows soaking routines to be varied depending on the different classes of animals that may be located within a barn (i.e., a different routine for one side of the feed bunk vs. the other) or even multiple routines for various pens on either side of the bunk. This flexibility allows the tailoring of soaking routines to match the various classes of animals (dry, pre-fresh, high producers, low producers or even heifers in extreme environments).
So how much savings can this technology deliver?
The answer, as is the case with all technology, depends on where you are at present and how well the new technology gets managed. At first blush, simply the fact that each Smart Soaker™ acts independently and only cycles when cows are in range of its ultrasonic range would be an impressive reduction in water usage. Research on the daily time budget of cows has shown that on average cows only spend approximately 23% (5.5 hours) of their time at the feed bunk.5 We can deduce that “on the average” feed bunk soakers should be idle the other 77% of the daily time budget. Interestingly that number is eerily close to Dr. Harner’s earlier referenced projection of savings that may be possible! Water savings is not the only money to be accounted for. Since we already know the cow’s budget has her away from the feedbunk 77% of the time on the average, it makes sense that during heat stress times, this technology will deliver soaking to the cow EVERY time she presents herself to the feedbunk, making the process markedly more efficient and thereby should contribute to increased comfort and milk production.
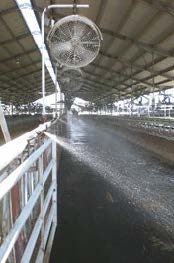
Precisely how much reduction in water use across a herd would depend on a variety of factors such as milk production levels, dry matter intake, ration palatability, and feed bunk management in general. In other words, the more time cows spend at the feed bunk, the more often the soakers are active. To be clear, restricting water usage for soaking when the THI in the cow’s environment calls for it is in no way efficient. Rather, it is counterproductive. The approach is to restrict water only when the THI indicates that soaking is not needed, or when there are no cows present. (See Figure 3.) Since the Smart Soaker™ is always on but operational only when cows are present, soaking activity is suspended while cows are away from the pen. Don’t laugh. I have seen soakers functioning (spraying on concrete) on standard timers when pens were totally void of cows – not simply at the parlor for milking!
Stacking Efficiencies Could Be Huge
As big as the savings discussed to this point could be, let’s take it one step further. Higher producing cows typically spend more time at the feed bunk to achieve higher dry matter intake to support that production, right? With the Smart Soaker™ , dairy farmers can manage soaking routines by pen to maximize cooling and theoretically encourage even higher dry matter intake/milk production for the cows most likely to show a response. It is this feature of the technology that may provide significant increases in efficiency not only in more efficient water use (savings), but in increased feed intake, better feed conversion and increased milk production (income).
Related to the valid concerns over the avoidance of feed intake interruption, the Smart Soaker™ is programmed to pause or delay water application upon identifying an animal in range, allowing cows the opportunity to avoid being sprayed in the face, which we all know cows do not like. If cows back out of range, the sensor immediately ceases to spray, allowing them or other cows to gain access to the feed bunk if they so desire without discouragement.
Improvement Over “One size fit all…”
Simply reducing the length of the “on time” to prevent runoff (as opposed to just wetting the cow) will in fact save water. However, doing so usually means having to increase the number of cycles per hour to cover the highest number of cows in the pen. The increase in the number of cycles erodes some portion of the water savings. You still have the issue that if a cow is not present, the water hits the floor. In contrast, the Smart Soaker™ programmable technology eliminates this issue when coupled with its ultrasonic sensor that is the ultimate determination of dispensing water or not.
The programmable feature of the Smart Soaker™ allows the “on time” to be set to a length of time aimed precisely at wetting the cow to the point of runoff and then shutting down. Likewise, the “off time” can be set to whatever length of time estimated (depending on ambient conditions) for the cow to dry and ready to benefit from another round of soaking. And again, remember that each device on the entire line operates independently rather than all the units cycling together. Lastly, if a cow backs out of range and another cow enters that space, the device resets itself and provides cooling to the new/next cow as programmed, eliminating the need for her to wait for the entire system to recycle as in conventional installations.
Directly to this point, Rick Grant’s work at the Miner Institute concluded that the average dairy cow will spend 3-5 hours per day eating and that time is broken up into 9-14 “meals” per day.6 This would mean that a cow’s unimpeded trips to the feedbunk may last from 20-30 minutes each. Rather than waiting for a conventional system to activate a full line of soakers, many of which may have no cows present, the Smart Soaker™ acts (based on its settings) individually to alternately soak and allow drying multiple times during each meal, thereby maximizing the cooling benefit when a cow is present. Furthermore, since we already know that once a cow is “soaked to the skin” most of the additional water runs off the cow and hits the floor. Smart Soaker™ allows us to limit the application of water in subsequent soakings within a cycle so that cows can be alternately soaked and dried for the duration of her visit to the feed bunk when her micro-environment calls for soaking. One could deduce that this makes the cow more comfortable and encourages dry matter intake concurrently!
Technology Creates Possibilities
Illustrating further application flexibility of the technology, let’s talk about dry cows. Research over the past recent years has shown the indisputable beneficial impact of keeping dry cows cool during the dry and pre-fresh periods. Those benefits extend not only to the dry cow’s comfort and welfare in the current day, but to her future milk production, future reproductive performance, and even the future of the heifer calf she is carrying.7,8 But let’s be honest. Low milk prices and slim margins historically promote spending “cooling dollars” on milking cows first, and on many farms that is still the case. The technology provided by the Smart Soaker™ system makes huge sense in cooling dry and pre-fresh cows. The increases in cooling efficiency this innovative technology brings simply adds to the already favorable economics of cooling dry cows with a conventional soaking system support.
Here is another example of this technology’s flexibility that may fit certain operations. I have been on farms where I have heard, “I’d love to soak my cows, but my situation (i.e., lagoon space, land application restrictions, etc.) simply won’t allow me to add any additional water into the system.” The Agpro Smart Soaker™ could virtually eliminate this issue. With intense observations and fine-tuning of the settings, a dairy with such restrictions could program the device so that runoff would be negligible. Again, as mentioned earlier, responses from any kind of technology depend on how intensively it is managed. I am old enough to remember when TMR’s were “new technology.”9 And look how that has revolutionized the dairy feeding industry!
Closing the Gate
This new technology appears to provide the opportunity to inject a significant, measurable increase of efficiency into one of the most useful cooling techniques on the dairy farm today. As feed line soaking can be one of the largest uses of water on the farm, it should be considered in any setting where high temperatures prevail, and especially in those settings where high humidity concurrently exists. While the actual benefit your farm achieves obviously will depend on what you are doing currently and how well you manage the new technology, this system promises a massive reduction in freshwater use, a corresponding savings in lagoon space, and significant savings in waste disposal. Learn more about Smart Soaker™ at the Agpro website or by visiting their channel on YouTube.
1© 2000 – 2019. TheDairySite – Dairy Cattle Health, Welfare and Diseases News. 5m Publishing, Benchmark House, 8 Smithy Wood Drive, Sheffield, S35 1QN, England. 5m Enterprises Inc., Suite 4120, CBoT, 141 West Jackson Boulevard, Chicago, IL, 60604-2900, USA. – A Benchmark Holdings Plc. Company
2 Cooling cows efficiently with water spray: Behavioral, physiological, and production responses to sprinklers at the feed bunk – Jennifer M. Chen*, Karin E. Schutz†, and Cassandra B. Tucker*; *Department of Animal Science, University of California, Davis 95616; †AgResearch Ltd., Hamilton 3240, New Zealand. J. Dairy Sci. 99:4607–4618 © American Dairy Science Association®, 2016.
3 Effectiveness of Cow Cooling Strategies Under Different Environmental Conditions – Proceedings of the 6th Western Dairy Management Conference, March 12-14, 2003. Michael J. Brouk, Department of Animal Sciences and Industry, Kansas State University, 134 Call Hall, Manhattan, KS 66506-1600. John F. Smith, Department of Animal Sciences and Industry, Kansas State University; Joseph P. Harner, III, Department of Agricultural and Biological Engineering, Kansas State University.
4 10 simple ways to reduce dairy water waste – The Progressive Dairymen, Dave Natzke, Editor. Published May 22, 2017. From presentation of Dr. Joe Harner, Kansas State University. Presented at Western Dairy Management Conference, 2017.
5 Taking Advantage of Natural Behavior Improves Dairy Cow Performance, Dairy Cow’s Daily Time Budget. Rick Grant, W. H. Miner Agricultural Research Institute. Presented at 2007 Western Dairy Management Conference. Posted at extension.org.
6 Taking Advantage of Natural Behavior Improves Dairy Cow Performance, Dairy Cow’s Daily Time Budget. Rick Grant, W. H. Miner Agricultural Research Institute. Presented at 2007 Western Dairy Management Conference. Posted at extension.org.
7 Help Your Dry Cows Avoid Heat Stress Webinar – Dr. Geoff Dahl, University of Florida. March 2015. Hoard’s Dairyman Webinar Archives
8 Heat Stress Affects Heifers Even Before Birth – Dairy Herd Management, June 2019. Article by Maureen Hanson on research by Dr. Geoff Dahl, University of Florida.
9 Schingoethe DJ. A 100-Year Review: Total mixed ration feeding of dairy cows. J Dairy Sci. 2017 Dec;100(12):10143-10150. doi: 10.3168/jds.2017-12967. PMID: 29153159.